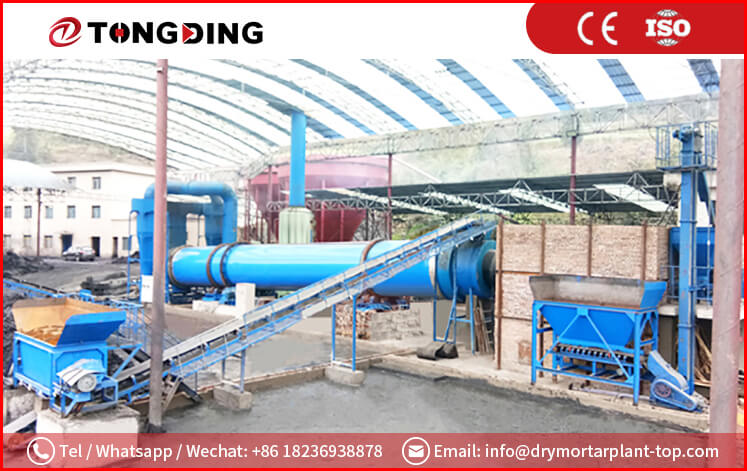
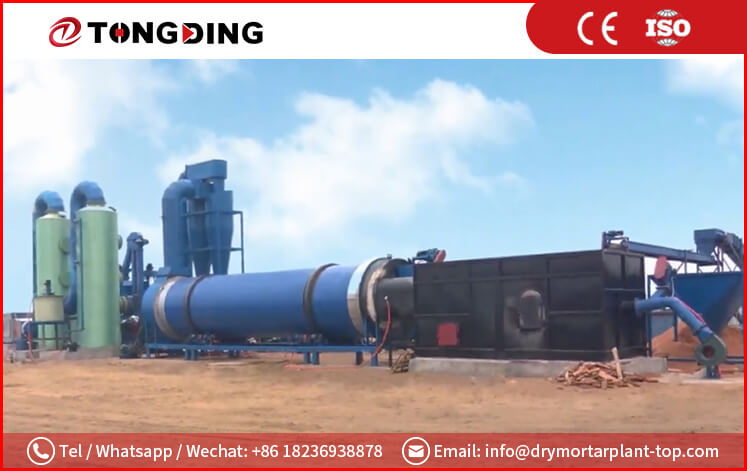
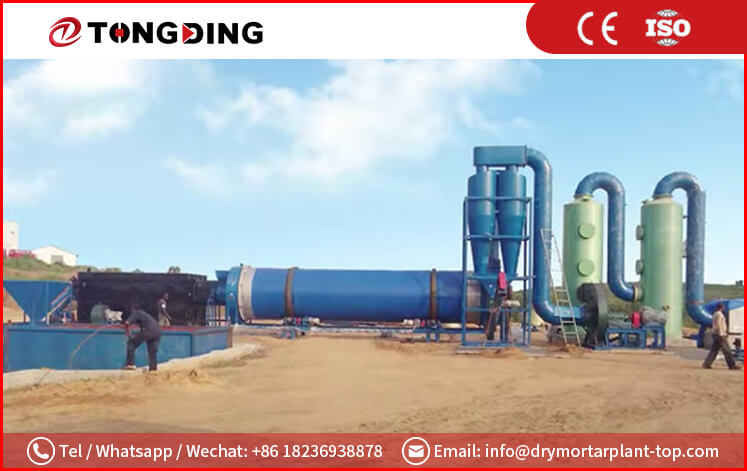
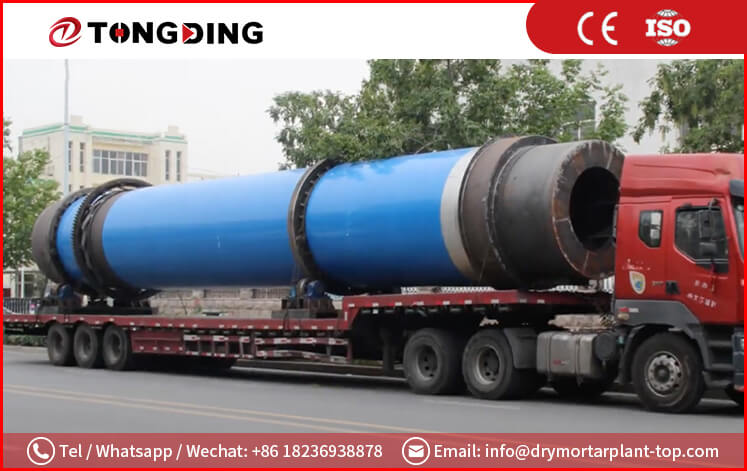
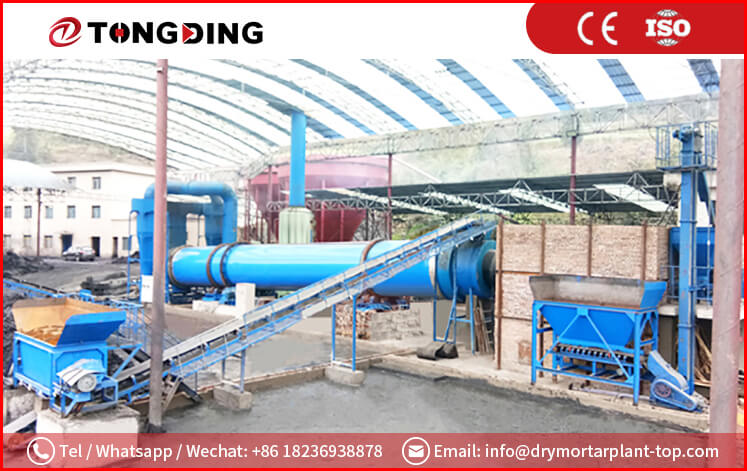
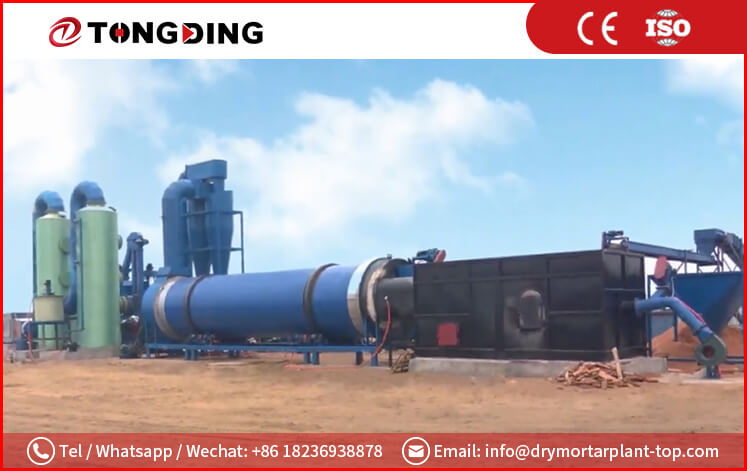
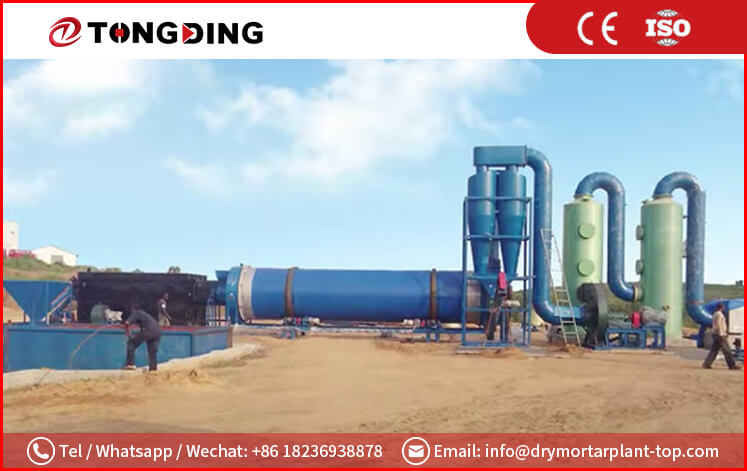
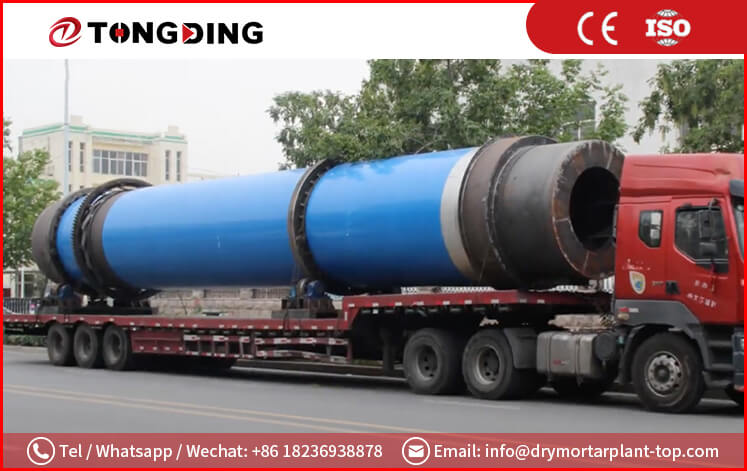
Coal Chemical Industry Rotary Dryer
Capacity: 200-2000 t/d
Heat Source:Suitable for biomass, natural gas, diesel, steam, coal, etc.
Application: Widely used for drying all kinds of coal, lignite, carbon coal, including anthracite, lean coal and poor lean coal, lean coal, coking coal, fat coal, air fertilizer coal, gas coal, etc.
Product Introduction
TongDing is a Chinese coal slime drying industry enterprise that integrates design, production, and sales of drying equipment. With nearly 20 years of rapid development, it has emerged as a leading brand in China's drying equipment industry. The company focuses on the current coal and blue carbon industry market, conducts technical research, practical case studies, and has developed the coal chemical industry of coal and blue carbon drying drum system before carbonization. This system is often used in LAN charcoal half coke dry quenching cooling, recycling heat energy or in LAN charcoal carbon coal cooling and dry raw material coal series to fully recycle hot charcoal carbon coal heat and remove coal moisture to a greater depth. This equipment has advanced technology, stable operation, and is easy to operate and maintain.
This type of equipment is suitable for drying all kinds of coal, carbon coal, charcoal, anthracite coal, lean coal, coking coal, fat coal, air fertilizer in coal, gas coal, weakly caking coal, non-sticky coal, long flame coal, lignite, coal washing, screening, raw coal, bituminous coal, tail coal, and coal fines. The equipment can be customized according to customer requirements.
Coal drying technology is divided into two types: drum drying and drum distillation units. Drum drying uses a rotary drum dryer to reduce the moisture content of coal, resulting in high heat value quality coal. Drum drying distillation technology combines a rotary drum dryer and a rotary distillation machine. The dryer dehydrates and heats the coal while the dry distillation machine removes the volatile parts and internal moisture of lignite, resulting in high heat value, low sulfur, low moisture, and low volatile dry distillation upgraded coal.
Layout Reference
Working Principle
There are two types of technologies used in the coal drying industry: drum drying and drum distillation. Drum drying involves the use of a rotary drum dryer to reduce the moisture content of the coal, resulting in high-quality coal with a high heat value. On the other hand, drum drying distillation technology involves the use of both a rotary drum dryer and a rotary distillation machine. The dryer dehydrates and heats the coal, while the distillation machine removes the volatile part and internal moisture of the lignite through dry distillation. The product obtained is an upgraded dry distillation coal with high heat value, low sulfur, low water moisture, and low volatility.
The coal and blue carbon drum dryer is composed of several components including the heat source, belt feeding machine, rotary drum, belt discharging machine, induced draft fan, cyclone dust collector, bag filter, nitrogen or carbon dioxide gas oxygen concentration prosecution explosion-proof security system, power distribution, and temperature, pressure, oxygen concentration, speed interlocking spreading system. The equipment adopts countercurrent (or downstream) drying technology with the following working principle:
Wet material enters the drying drum and is divided into the following work areas:
1.Feeding area: The coal quickly evaporates moisture in this high-temperature area, and the material is guided by a large angle plate and then imported into the next workspace.
2.Copy plate area: In this area, the coal is lifted by copy board and forms a curtain material status. The coal temperature gradually increases to 150-250 ℃ (depending on the type of coal). At this point, the material has good contact with hot air, and the moisture in the coal rapidly evaporates and becomes water vapor, which is siphoned off by the induced draft fan, achieving deep drying. The coal in this area is dried to a moisture content of less than 5% (or much lower), with a loose state. After the heat exchange, the material achieves the required moisture state and enters the final discharging area.
3.Discharging area: This area does not have a copy plate. The material is transported by scroll to the discharge port to complete the entire drying process.
Parameter
Model | Φ2.4x24m | Φ3.0x30m | Φ3.2x32m | Φ3.6x36m | Φ4.0x40m |
Inner diameter (mm) | 2400 | 3000 | 3200 | 3600 | 4000 |
Length (mm) | 24000 | 30000 | 32000 | 36000 | 40000 |
Power (kW) | 37 | 75 | 132 | 280 | 315 |
Inclination (°) | 0-5 | ||||
Shaft rotational speed (r/min) | 2-4 | 1-3 |
Inquiry
Please Feel free to give your inquiry in the form below. We will reply you in 24 hours.