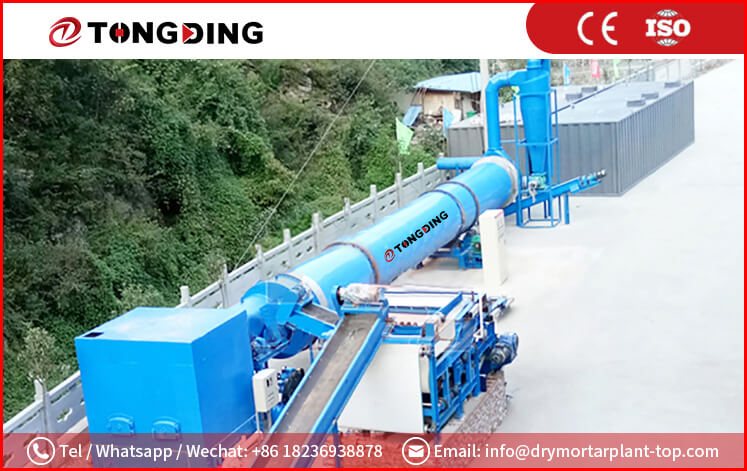
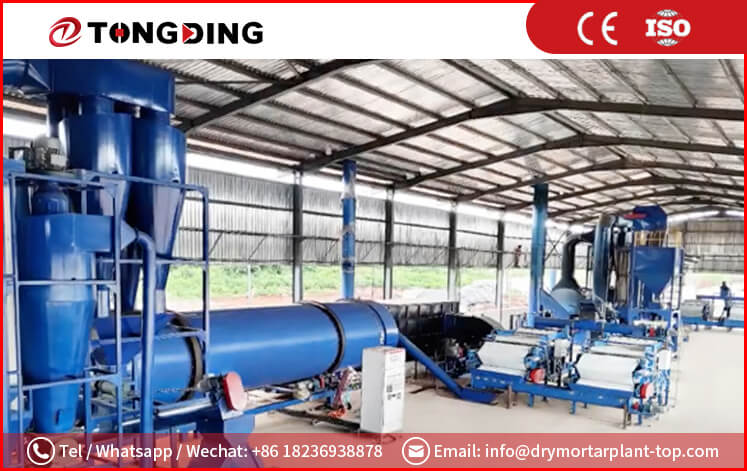
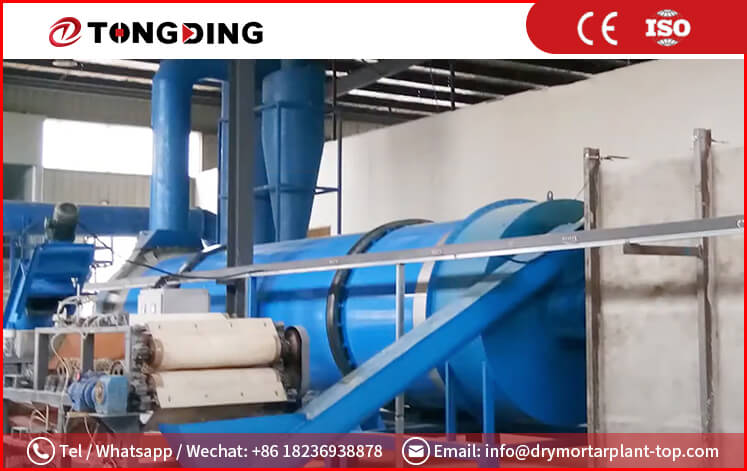
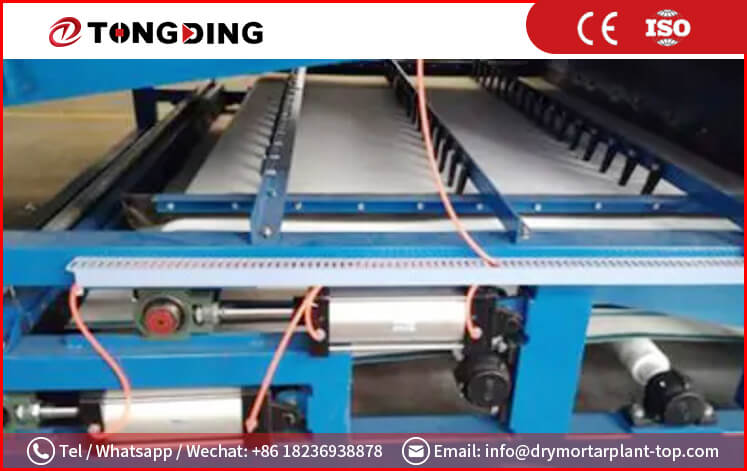
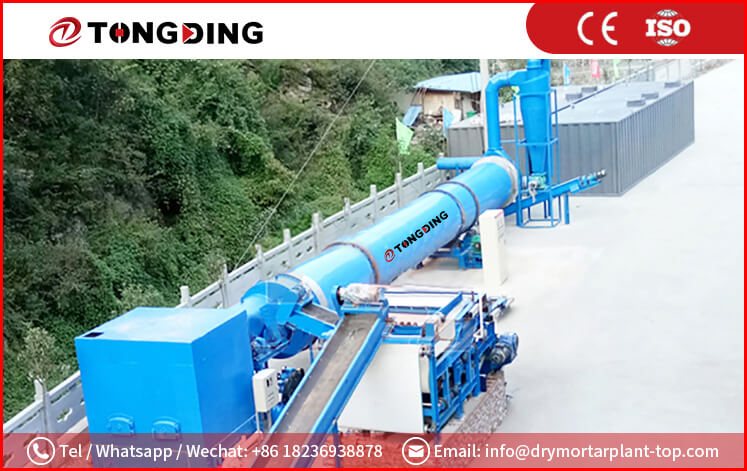
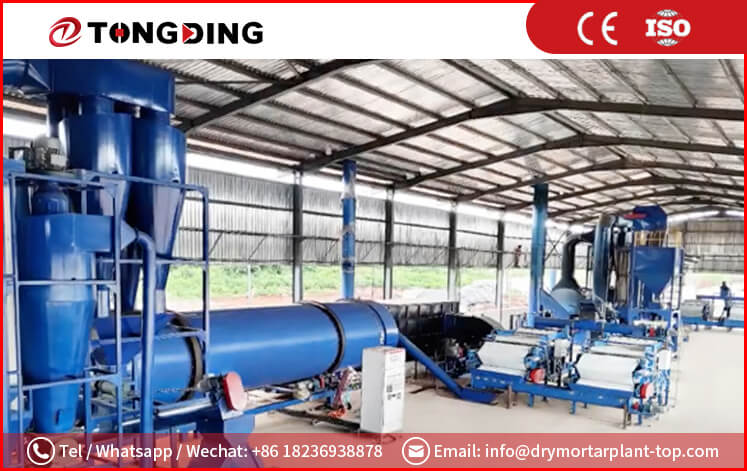
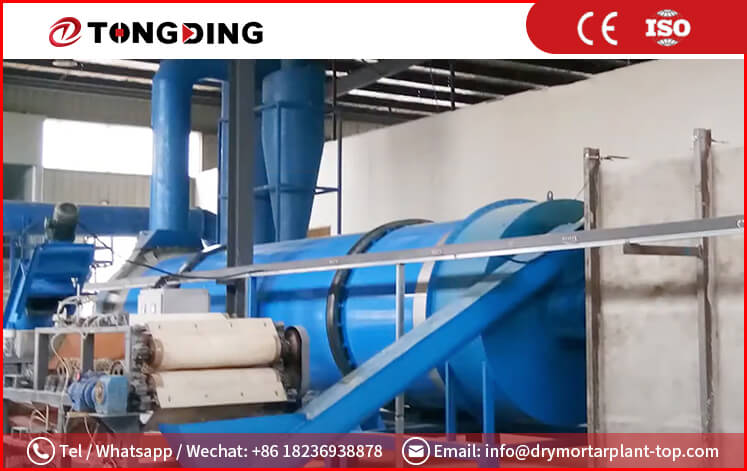
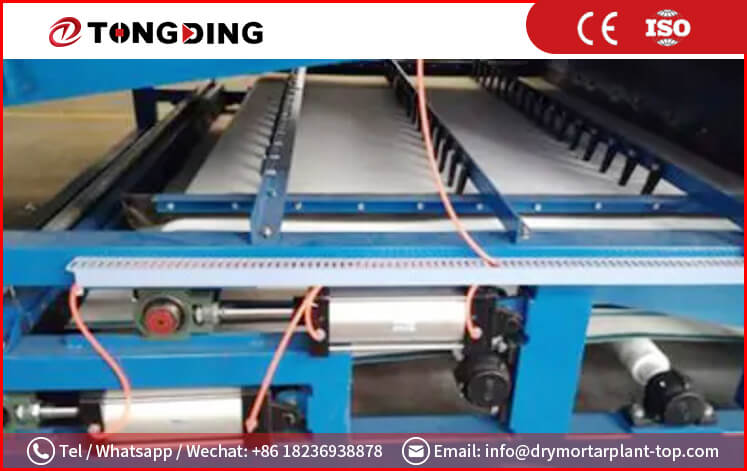
Potato Starch Residue Dryer
Capacity: 43.7-317.6 t/d
Heat Source:Suitable for biomass, natural gas, diesel, coal, etc.
Application: Widely used for drying potato residue, sweet potato dregs, cassava residue, tapioca slag, and other agricultural products produce starch production.
Product Introduction
With a moisture content of around 80%, potato residue and starch residue exhibit high viscosity due to their moisture content, making them difficult to dry with traditional drying equipment. High drying temperatures can cause slag starch gelatinization, resulting in dextrin clogging material particles' pores, and preventing water evaporation. This leads to the surface of the particles turning yellowish-black, causing a serious impact on the sale of dry residue. Conversely, low drying temperatures cannot effectively reduce the moisture content to below 15%, causing the dryer to become sticky, leading to gelatinization and agglomeration. The drying equipment is thereby unable to perform normal production, leading to a negative impact on customer interests.
To address these issues, Dingli brand starch slag dryer has been developed based on extensive research and development of raw materials such as cassava and potato slag. Drawing from years of dryer production experience, the dryer is capable of drying all types of potato residue below 10% moisture content in a single pass. The company utilizes a "mechanical dehydration + drum drying + pulse air drying" special Chinese patent technology to effectively solve traditional dryer problems associated with drying cassava and potato residue. The result is a drying process that yields materials with a perfect color and excellent quality, and an energy-efficient and environmentally-friendly production line that operates safely and stably. The equipment has received high praise from numerous new and longstanding customers.
Layout Reference
Working Principle
Material flow: The material with a moisture content of 75-85% is subjected to a special dehydration machine to remove a part of the moisture, reducing it to around 68%. It is then conveyed by a screw conveyor and sent to the dryer for downstream drying. The material is constantly taken and scattered in a spiral forward method by the inner shoveling plate. The mixing blade device inside fully stirs and crushes the material, which undergoes full heat exchange with the hot air resulting in the rapid evaporation of water vaporization, reaching about 35%. The dried material is discharged by the screw conveyor and sent to the semi-wet material crusher where it is crushed to a size below 1mm. The material is then subjected to the pulse air-drying process, where it is quickly dried to 12% by the cyclone discharger, and the pulse bag dust collector recovers the dry powder. The exhaust emissions amount to the national standard requirement, thus completing the entire drying process. To prevent the material from adhering to the cylinder wall, a drum cleaning device is installed inside the drum.
Airflow: The air is inflated through the hot blast stove fan and enters the hot blast stove for combustion heating. Its temperature reaches up to 600-850℃ and is then absorbed by the dryer induced draft fan to dry the material and evaporate water. The material undergoes heat exchange drying, and when the temperature decreases to 55-85℃, it is discharged out of the dryer. Wet dust is discharged through the cyclone and the pulse dust collector, which purify and emit it according to standard.
Parameter
Specification |
Input Capacity(t/d) |
Output(t/d) |
Evaporation Capacity(t/h) |
Total Power(kw) |
Total Weight(kg) |
Area |
Raw Material Moisture(%) |
Dried Material Moisture(%) |
Drying temperature(℃) |
TDFPZ257 |
43.7 |
25.7 |
0.75 |
55 |
25000 |
5m*20m |
(Mechanical dehydration to around 68%, and then dry by dryer) |
10% (adjustable) |
350-450℃ |
TDFPZ309 |
52.5 |
30.9 |
0.90 |
75 |
27000 |
5m*20m |
|||
TDFPZ446 |
75.8 |
44.6 |
1.30 |
95 |
28500 |
6m*22m |
|||
TDFPZ994 |
169.0 |
99.4 |
2.90 |
140 |
33500 |
8m*25m |
|||
TDFPZ109 |
186.5 |
109.7 |
3.20 |
170 |
38500 |
8m*25m |
|||
TDFPZ126 |
215.5 |
126.7 |
3.70 |
210 |
45000 |
10m*28m |
|||
TDFPZ154 |
262.2 |
154.2 |
4.50 |
260 |
60000 |
10m*30m |
|||
TDFPZ186 |
317.6 |
186.8 |
5.45 |
300 |
80000 |
10m*30m |
Hot Products:
Inquiry
Please Feel free to give your inquiry in the form below. We will reply you in 24 hours.